 |
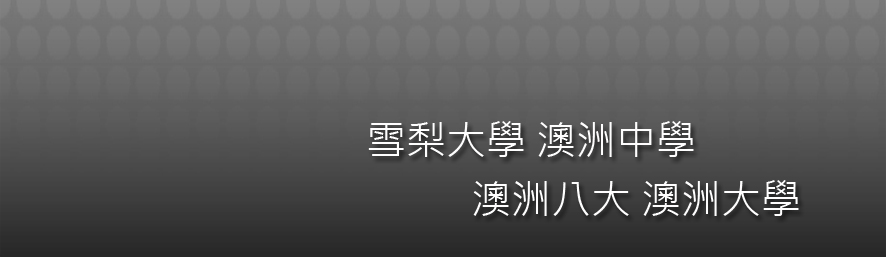 |
|
最新消息
>
十八種日本鑄造產業的新技術
|
 |
文章来源:http://www.sohu.com/a/201153605_785602
原標題:十八種日本鑄造產業的新技術日本素形材雜志每年的第一期都專門介紹上一年的新技術發展,稱之為"雜志上的新素形材展覽"。2002年鑄造方面共介紹了22種,其中有2種獲得了政府及有關部門的獎賞。現簡介如下:一.利用鑄鐵特性制成的高音質揚聲器揚聲器的構成主要有:擴聲部分、電路和外殼。特別是在外殼方面,為了徹底控制其達到不振動,利用了下述三種鑄鐵。◆高碳片狀石墨鑄鐵。石墨含量高,且石墨片長的鑄鐵。◆共晶石墨鑄鐵。用連續鑄造法制造的共晶石墨鑄件,從內部到外部都具有細密組織。◆鑄鐵粉。鑄件拋丸清理的廢棄物。外殼部分用鑄鐵制成的部件有三項:1.安裝低音喇叭用的鑄鐵環。在喇叭與前板之間裝高碳片狀石墨鑄鐵環,既提高剛性又可減振。2.鑄鐵制豎振子和鑄鐵制減振桿,在項板上裝共晶石墨鑄鐵棒形振子,并用減振桿固定前板、側板和里板。3.鑄鐵粉夾層板。將鑄鐵粉制成片狀夾在兩配線板之間。由于在以上三種構造上下了功夫,抑制了外殼的有害共振,低音喇叭振動板忠實按輸入信號動作,從而使低音分辨能力達到前所未有的水平。二.大型矩形球鐵隧道結構段采用矩形斷面的框架,與圓形斷面框架相比,隧道內空間可以有效利用,掘土量也可以減少。但比圓形結構段的彎矩大,因而要求有高的強度,也會有由于形狀復雜而致費用高的問題。為了解決這個問題,日本京都地鐵東西線上首先采用了大型矩形斷面框架結構段。隧道由無中柱的連接部分(57米)和有中柱的一般部分(703米)構成。一般部分采用球鐵鑄造的結構段。有中柱的矩形斷面結構段,中柱與框架外圍接連部有很大的彎矩。據此斷面力來決定整體的斷面是不經濟的。因此僅在中柱的結合部用抗彎曲強度高的波形斷面,其他部位用經濟的四柱梁斷面。經過實物的環形載荷試驗,彎矩、軸向力及變形分布等實測值與分析值基本相近,證明構造是安全的。三.耐磨的高合金麻口細晶粒鑄鐵軋輥帶材熱軋機用的工作輥,前段到中段臺架都可用耐磨性好的低合金鋼軋輥。但后段臺架用低合金鋼軋輥就有可能發生事故的問題。現在也使用耐事故性好的高合金麻口細晶粒鑄鐵軋輥。為保持其耐事故性同時進一步提高其耐磨性和保持表面質量的能力,開發了新型的高合金麻口細晶粒鑄鐵軋輥。新型軋輥的金相組織(面積比)是:30-40%的滲碳體,2-5%的石墨,其余為硬度HV480-520的基體。新型軋輥中加入了原先高合金麻口細晶粒軋輥中沒有、而低合金鋼軋輥中含有的合金,并調整了化學成分。低合金鋼中的合金,能和碳結合結晶出高硬度的MC型碳化物。另一部分固溶于基體中,強化基體。基體的硬度由原來的HV512提高到新開發的HV568,提高了11%。為提高耐磨性而添加的低合金鋼中含有的合金,是白口形成元素,因而會阻礙石墨結晶析出,而石墨又是保持其耐事故所必需的,因此對成分進行了調整。新開發的軋輥(軋鋼2000噸)與過去的軋輥(軋鋼1250噸)軋鋼后,對表面進行了檢查,確認新開發軋輥的磨損比過去的軋輥要少。而且過去的軋輥表面粗造度為11.9μm,新產品為Rmax6.9μm,表面質量也有了改善。耐磨性用每磨損1mm的軋輥量來評價,新軋輥是過去軋輥的130‰。四.可焊接、可熱處理的薄壁壓鑄摩托車架摩托車的車架此前多是用板材、擠壓的型材或者鍛材制成的部件和重力鑄造的鑄件焊接組裝構成的。但是,用板材和型材作出自由曲面受到一定的制約,重力鑄造在大型化和薄壁化方面也受到限制。從車架設計方面說來,最好能作出理想的自由曲面,在強度上必要的部分厚一些,不必要的部分盡可能薄些,達到輕量、高剛性構造。因此,研究開發了薄壁大件也可成形,通過熱處理可獲得充分的強度和伸長率,而且可焊接組合的壓鑄件生產技術,并應用于摩托車車架。壓鑄是通過柱塞和缸體將鋁液高速注入壓型,能復制精度好的薄壁鑄件而且成形效率高的鑄造技術。不像板材、型材那樣鑄造后需要壓伸、擠壓等二次加工,壓鑄可以直接成形,從而可降低成本,能耗,對環境影響小。但是,一般壓鑄時,烙液中易于卷入空氣和氧化物,制品中含氣量高、缺陷多,進行T6熱處理和焊接有困難。而且,薄壁部分凝固快,大型薄壁化時在填充性上也受到制約。針對上述問題采用了以下措施。1.壓型密封和真空排氣,壓型內達到5Kpa程度的高真空時進行鑄造,以抑制高速澆鑄時卷入空氣。2.控制壓型溫度,薄壁時提高鋁液流動性,可成形大件。3.根據鑄件的形狀和壁厚,精確控制澆注速度,減少紊流。4.鋁溶液凈化處理,減少活塞一缸體間的潤滑劑,以極力控制產品中混入不純物質。5.用計算機對流動、凝固進行模擬分析以取得最佳的壓型設計方案。采用以上措施后,壓鑄件的含氣量在3ml/100g以下,與重力鑄造的鑄件相當,可進行T6熱處理和焊接。一般鑄件壁厚以2.5mm左右為界限,現在壁厚1.5mm的也可成形,最大尺寸可到1.5m。五.與透平罩殼成一體的排氣岐管。在世界規模的競爭中,汽車零部件降低造價是重要的議題。在鑄造方面,重要任務之一就是從設計自由度著手,發展一體化、中空化,以達到輕量化,降低造價的目的。將汽車發動機的透平罩殼和排氣岐管一體化,從而省掉兩者相連結的法蘭等零部件,使重量減輕20%,造價降低30%。透平罩殼鑄件要求有耐高溫氧化性和耐生長性,而排氣岐管則主要是熱疲勞的壽命問題。要解決這二個方面的要求。在鑄鐵表面形成富硅層,可以提高耐高溫氧化性,經試驗加4%的硅即可達到此目的。而硅量在3.8%以上時,也可滿足耐生長性的要求。熱疲勞壽命受制品形狀和使用環境影響很大。大體上說,硅量在3.5-5%時(特別是最高時)在各種條件下均可達到提高熱疲勞壽命。球鐵含硅在4%以上時,有過共晶的傾向,應注意鐵水的流動性和產生石墨漂浮的問題。對此,碳當量(C+1/3Si)宜在5%以下。因此,硅量在4-5%,碳量在3-5%以下時,可滿足兩方面的要求,而達到透平頂罩殼與排氣岐管整體鑄造的目的。六.纖維增強的發動機缸體汽車的發動機要向輕量化、緊湊化、高性能化方向發展。輕量化主要是發動機中最重的缸體使用鋁合金,緊湊化主要是縮短缸體的各缸孔間的尺寸,以達到使缸體全長縮短。高出力是同樣的缸體使缸徑擴大從而增大排氣量,這與簡潔化是兼容的。高性能化是使缸體整體鋁合金化,使缸孔的熱傳導好、變形小,從而提高發動機效率,節約能源。原來的缸體多用鋁合金壓鑄,鑲鑄鑄鐵缸套,不能滿足上述要求。因而開發了整體鋁合金發動機缸體,缸孔部分用纖維增強金屬。缸孔部分用陶瓷纖維預制品,其間隙中浸入鋁合金液體,置換空氣而形成。預制品在壓型中定位,與過去用的鑄鐵襯套同樣。將預制品進行預熱,固定在支撐物上,支撐物在壓型中定位。另外,為使預制品的纖維間隙易于浸入鋁液,采用層流壓鑄法。為防止鋁液溫度降低,向壓射室涂敷粉狀潤滑劑,壓型上涂敷粉狀離型劑。鑄造后可將支撐物回收反復使用。七.降低制動噪聲的高衰減制動鼓材料近來對汽車制動噪聲的要求愈來愈嚴,在開發高性能制動材料時,在要求改善其可信賴性和耐久性的同時,也要提高其衰減性能。首先在其化學成分的選定上要使其在衰減性、強度、耐熱裂等方面都有優良性能。材料的化學成分及力學性能
關鍵字標籤:離心鑄造
|
回上頁 |
|
|
|
|
關於澳洲│留學資訊│澳洲學校│留學問題│聯絡我們│最新消息│網站導覽│回首頁
日本留學,家教,多益,多益,家教老師 |
|
 |